What is the difference between Industry 4.0 and the Internet of Things (IoT)?
The technologies of today are numerous, complex and always abbreviated with acronyms: AR, VR, AM, IdD, AI. What does it all mean? (resolution: Augmented Reality, Virtual Reality, Additive Manufacturing, Internet of Things and Artificial Intelligence).We're often asked for explanations of terms. The difference between Industry 4.0 and the Internet of Things (IdD) is one of the most common questions. To put it simply, the Internet of Things is just one part of Industry 4.0, just as AI, Big Data and 3D printing are also part of it.In this article, you will learn what Industry 4.0 is, which technologies are part of it and how they are applied.
What does Industry 4.0 mean?
The term Industry 4.0 refers to the result of the fourth industrial revolution. The fourth industrial revolution is characterized by a combination of automated, traditional manufacturing and industrial processes with intelligent technology and machines that communicate with each other independently.
For instance, machines that are independent of each other in a production chain can now detect and rectify errors in production independently and optimize processes. The term Industry 4.0, abbreviated I4.0 or simply I4, originated in 2011 from a project of the German government, which immensely promoted the digitalization of manufacturing processes over the last two decades.
Industry 4.0 using the example of a fictitious clothing factory
Let's imagine an automated clothing factory. In this factory, a weaving machine continuously processes yarn into fabric. This fabric is then passed to a cutting machine via an assembly line. Once the fabric has been cut, a sewing machine sews it together to form a T-shirt. Finally, the inspection machine checks that the T-shirt is actually the desired size. Now the control machine notices that the T-shirt still retains the same size when reduced by two percent. The control machine communicates this information with all the other machines in the production line, and an artificial or machine intelligence is now used to jointly search for a solution.
The sewing machine indicates that it can turn over one millimeter less fabric without any loss of quality.The cutting machine receives this information. From now on, the machine cuts the fabric more briefly, the sewing machine folds over one millimeter less and the T-shirt is two percent smaller.The end product is of the same quality, but the material costs are reduced by two percent. With a production of several thousand T-shirts a day, the costs saved are considerable.
This optimization can be carried out by the machines independently and without the assistance of any human being. This is known as self-optimizing value chains or the Smart Factory. That is Industry 4.0.
The history of Industry 4.0
The industrial revolution
During the 18th century, people began to use a combination of steam power and mechanical production equipment. Instead of a single worker at a spinning wheel, it was now possible to use dozens of machines working with consistent efficiency.
Leveraging steam power for industrial purposes was mankind's greatest breakthrough to date in increasing productivity. It became possible for the first time to produce more without having to spend more time on it.
However, steam power was not only used to manufacture products, but also to transport them. Steam-driven locomotives and steamships made it possible to trade over long distances.
The second industrial revolution
In the 19th century, we discovered electricity and the use of assembly lines for mass production. Henry Ford observed pigs being carried from butcher to butcher on an assembly line in a Chicago slaughterhouse. Every butcher did the same part of the slaughtering for every pig over and over again. That division of labor was transferred by Henry Ford to the production of cars, thus initiating the second industrial revolution.While an entire automobile used to be assembled at one station, the vehicles were now produced in partial steps on the conveyor belt. This was much faster, of higher quality due to the specialization of the individual workers, and ultimately even more cost-effective.
The third industrial revolution
The third industrial revolution began in the 1970s when computers were used to semi-automate the industry. Since the introduction of these technologies, we have been able to automate an entire production process and operate it without human assistance. Well-known examples of this include robots that carry out programmed processes independently.
Industry 4.0
We are currently in the fourth industrial revolution. Due to our technological progress, machines can now independently record information, interpret it and communicate with each other.Network connectivity is added to machines that already contain computer technology. Then, a digital twin of this machine is created. That means, a digital 1:1 copy of this machine is created. This digital twin allows them to send information about themselves and receive information and commands from other machines and their digital twins.
In this way, production can be analyzed and optimized in far greater detail and efficiency without human intervention.
The Technologies of Industry 4.0
The fictional clothing factory and its optimization are based on many different technologies. The Boston Consulting Group has defined nine pillars on which Industry 4.0 is built.
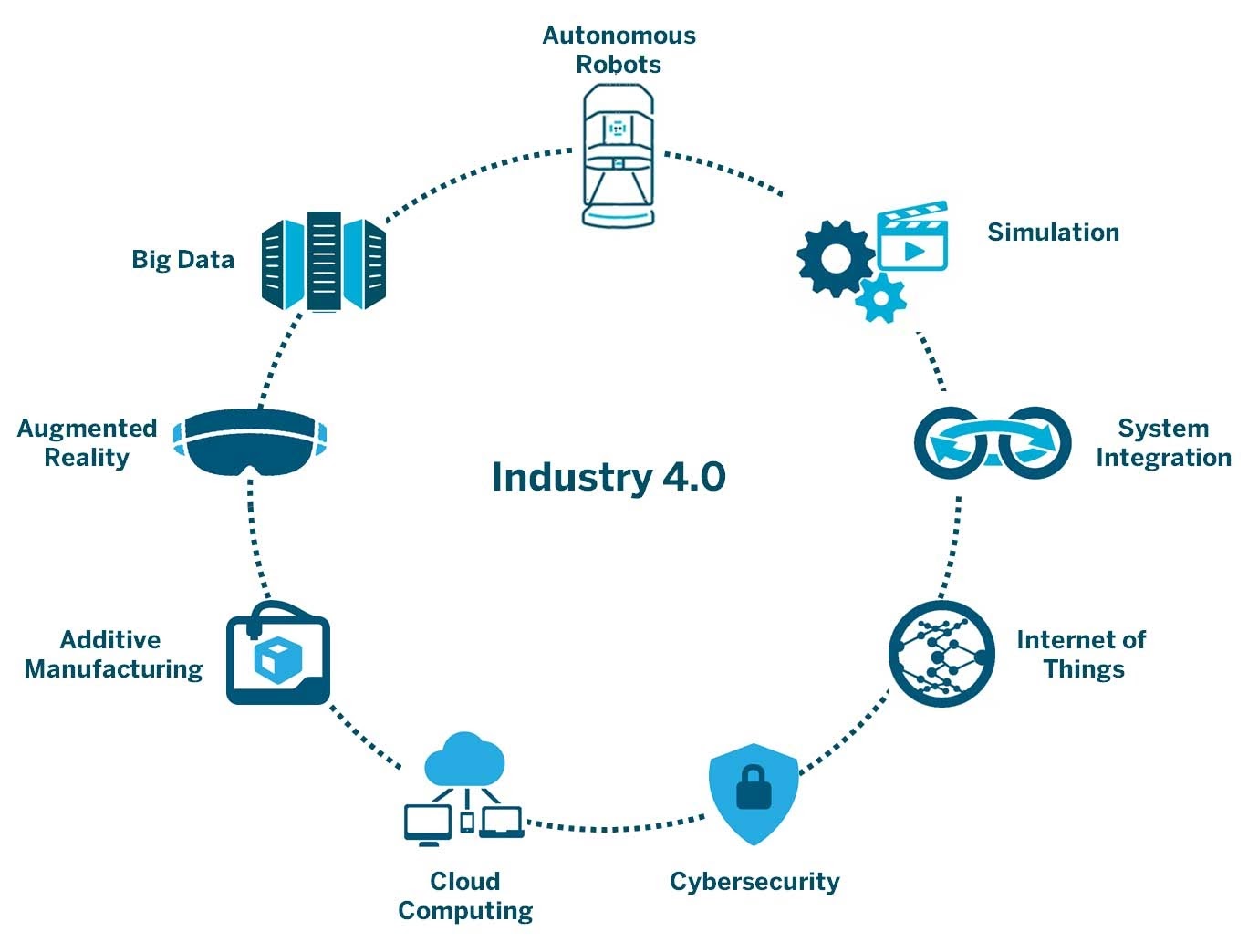
Additive Manufacturing
3D printing, also known as Additive Manufacturing (AM), refers to all manufacturing processes in which three-dimensional objects are "printed" - i.e. the material of an object is applied layer by layer by means of a printer. According to a Bitkom survey from 2019, one-third of German industrial companies already use 3D printing.
The reasons are obvious: countless individual parts are often used to manufacture a product, which are cast, milled and pressed by various machines. With a smart 3D printer, a manufacturing facility can produce all of the parts itself in suitable quantities instead of purchasing them from a distributor. Even if machine parts wear out or suffer a defect, a 3D printer provides a quick remedy.
Augmented Reality (AR)
By Augmented Reality we mean the extension of how we perceive reality with the help of computers. In terms of Industry 4.0, this involves supplementing images and videos with additional information provided by a computer. This information is superimposed on the images and videos or overlays real objects. We are familiar with this from soccer on TV - for example, when strategic moves are "traced" or the distance of a free kick is shown with a line.
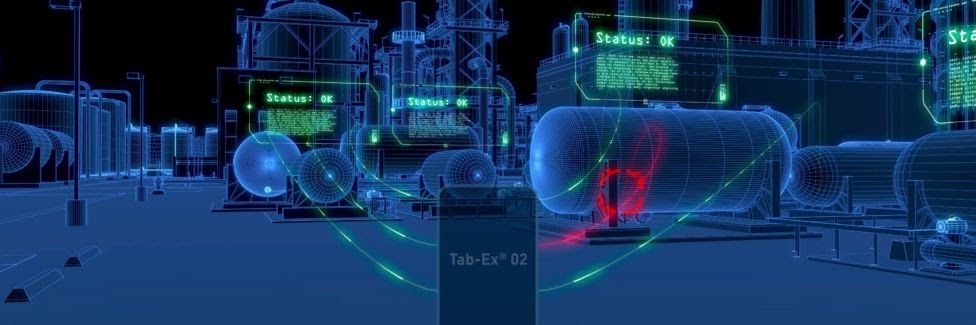
Augmented reality is being applied from industry to architecture, art and the military. Practical applications in the industrial sector would be navigation in buildings (e.g. for the maintenance of industrial plants) or providing information about the states of machines in the production line.
Autonomous Robots
Autonomous Robots (Autobots) are robots that perform tasks or behaviors with a high degree of autonomy and without human supervision. They range from robotic vacuum cleaners to autonomous helicopters. These are often found in warehouses and the manufacturing industry. Here, they improve the speed as well as accuracy of routine operations, reduce the risk of injury to workers in hazardous environments, and make physically heavy tasks such as palletizing products easier.
Big Data and Big Data Analytics
The amount of global data is increasing rapidly. While in 2018 it was still 33 zettabytes (1 zettabyte = 1 billion terabytes), 175 zettabytes are already predicted for 2025. This means that the volume of data will increase fivefold worldwide. A strong driver of this is the Internet of Things. For comparison: an autonomous car will generate around 1-4 terabytes of data per day in 2020.
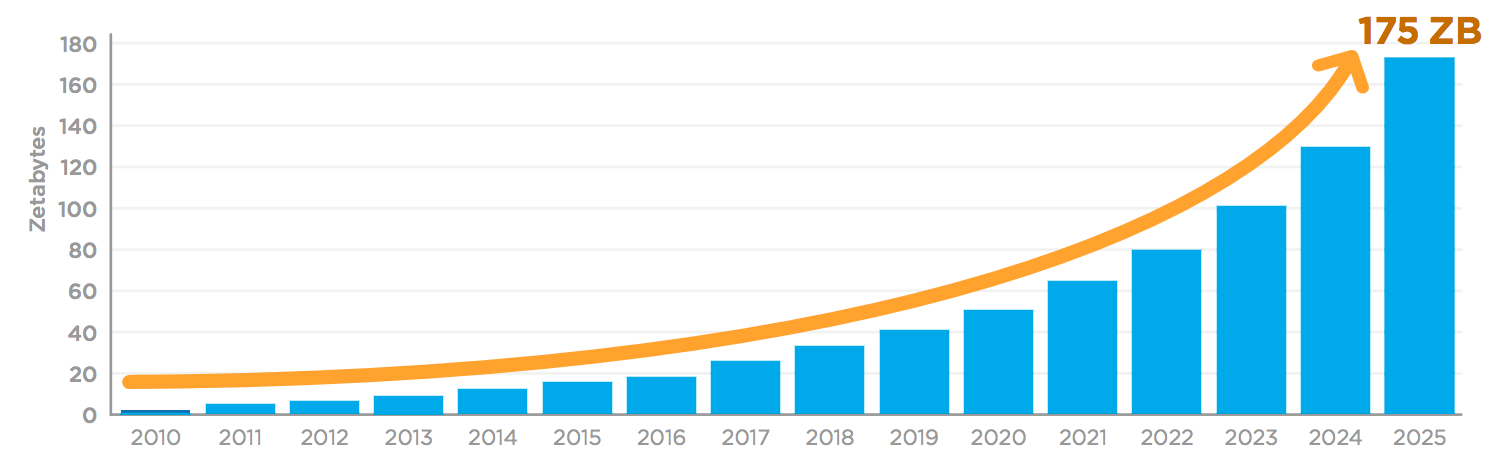
In the wake of Industry 4.0, production machines, robots and systems are recording detailed data at every step. Accordingly, this generates a huge amount of data, so-called Big Data. Machines must be able to read and process this data (Big Data Analytics), then apply it for direct implementation and optimization (see fictitious sewing factory) and store it securely. The prerequisites are high-performance software and hardware systems that often rely on artificial intelligence and cloud computing (computing power and storage space via the Internet).
Cloud Computing
Cloud computing, often only referred to as the "cloud", is an IT infrastructure that is usually provided via the Internet. Services are cloud storage and cloud computing. As mentioned above, the required computational power and storage capacity for AI and Big Data can easily outstrip the resources of most production sites. Therefore, cloud computing is practically a necessity for a working Industry 4.0.
In addition to solving the resource problem, there are many other advantages of the cloud. For example, multiple production sites can draw from a single source, in case of fire at a production site, only the hardware would be destroyed, and in addition, data can be accessed from anywhere in the world.
Cybersecurity
When it comes to Industrie 4.0, all production touchpoints are digitally connected to each other through standardized communication protocols. On the one hand, this is precisely the strength of Industrie 4.0, but on the other hand, this connectivity also offers plenty of room for attacks. The number of attackers, from individuals to companies to government agencies, has multiplied over the past few years, and industrial espionage is thriving tremendously. A robust cybersecurity approach is therefore more important than ever. As office IT expands to include production IT, security experts have been developing strategic and, above all, holistic concepts.
Horizontal and Vertical System Integration
Horizontal and vertical system integration refers to the greater integration of companies, departments, functions and capabilities. In this context, networking between divisions and departments is regarded as vertical integration, and between companies as horizontal integration. The basis for this is digitization, which ensures the efficient exchange of data between employees (both internal and external), machines and workpieces. Digitization therefore also lays the foundation for self-optimizing value chains (e.g., fictitious clothing factory). Furthermore, business processes can be outsourced and company boundaries shift as a result (horizontal integration).
Simulations
As the name suggests, simulations are used in Industry 4.0 to map the physical world. This means that complex processes can be simulated very realistically before they are implemented in reality. That is why this methodology is used in mechanical and plant engineering.
For this reason, it is also important that machines can carry out simulations independently and analyze the results. Based on this analysis, the machines decide independently what, how and in what way will be carried out and implemented. Thus, not only extremely efficient new plants are realized, but existing plants can also be inspected and optimized.
Internet of Things (IoT) / Industrial Internet of Things (IIoT)
According to the Boston Consulting Group, the final pillar of the Industry 4.0 is the Industrial Internet of Things (IIoT), which in turn is part of the Internet of Things (IoT) and is often listed here. In the following section, we explain both terms.
What is the Internet of Things (IoT)?
The Internet of Things (IoT) enables physical and virtual objects to be linked with one another. Information and communication technologies make it possible for individual objects to collaborate with each other. A practical example: When I get home in the evening, the light in the house entrance should turn on automatically. The GPS sensor in my cell phone locates my position, registers my coordinates and compares them with those of my home. Once the coordinates match, my cell phone sends a signal to the light bulb in the house entrance based on the time of day, and the light bulb turns on. The communication between the cell phone and the light bulb is carried out via the Internet of Things.
What is the Industrial Internet of Things (IIoT)?
While Internet of Things is an umbrella term, the Industrial Internet of Things (IIoT) refers to the network of communication between industrial machines and devices without the intervention of humans. Basically, the industrial part of the Internet of Things. Communication between machines in the fictional industry 4.0 clothing factory described above is an example of IIoT. The only difference between the IoT and the IIoT is the scope of application. The IoT serves consumers and the IIoT serves industrial production.
How does the IoT work?
Another example: Actually, we should not speak of the Internet of Things, but of an Internet of Things. We integrate various devices into an IoT, which can then communicate with each other, but not with the devices outside this network. For example, my cell phone cannot communicate with my neighbor's IoT.
To explain how IoT works, we will use the fictitious example of Anna, David and their smart home:
7:00 in the morning. The light turns on. David is already awake, and is watching Anna opening her eyes. She loves coffee in the morning. David knows that, of course. He goes to the kitchen and serves her the already filled cup of fresh coffee by her bedside.
That simple, everyday morning ritual requires the communication of several devices. The core of this communication is a so-called smart home hub in the bedroom, which serves as the control center of the IoT.
Each device at home has a digital twin that is wirelessly connected to this hub. In this way, every device sends information to the hub and receives instructions back from it.
So, what is going on behind the scenes in Anna and David's smarthome?
At 7:00 a.m., David's cell phone sends a signal to the hub.
The hub sends instructions to the light bulbs and the coffee machine. The lights come on and the coffee starts brewing.
When David enters the kitchen, a sensor registers his movement and sends this information to the hub. The hub sends the command "Turn the light on!" to the light bulb in the kitchen.
As soon as David picks up the cup, the coffee maker sends this information to the Hub. Now when someone wants to order a cup of coffee via the app, they get the error message, "No cup found. Please provide a cup."
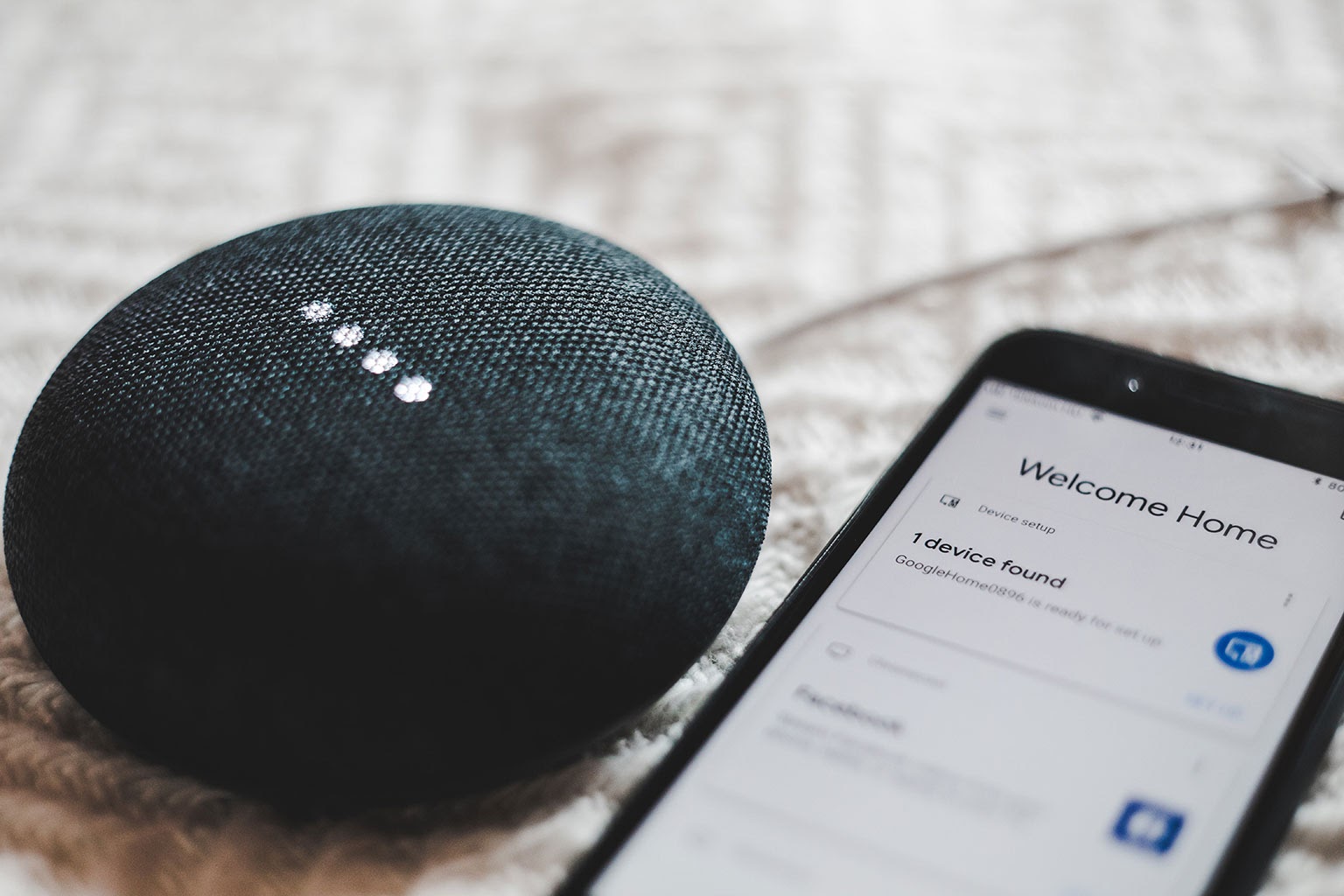
As humans, we began communicating with one another thousands of years ago. Now machines have taken this step as well. We pick up information through our senses, machines use sensors. We communicate physically - with our voice, writing and gestures. Machines communicate through an IoT.
In this way, our devices know where we are, what we are doing and what we will do next. To achieve this, artificial intelligence evaluates, for example, text messages, calendar entries, locations, or even a person's repetitive behaviour patterns, and uses this information to create a wide variety of predictive models that determine, by both relevance and probability, what our next move will be.
This interplay of technologies leaves open almost endless possibilities that go far beyond making our daily lives easier.
What are the risks and difficulties of IoT?
The S in IoT Stands for Security.
You read and hear this saying again and again in discussions regarding IoT. It sums up the biggest problem of IoT: lack of or poor cybersecurity. Imagine your coffee machine is infected with ransomware. It beeps incessantly, demanding a transfer of 0.1 bitcoin so you can drink coffee again. Or someone cracks the security system of your smart home, sets the thermostat to the highest level and disables your access to the system. There's nothing you can do except turn off the heat completely (and freeze) until the security issue is resolved.
However, the lack of cybersecurity isn't the only problem. The need for a continuous as well as fast network connection (in the case of autonomous driving) can also make your life miserable or, in the worst case, even fatal. If the Internet crashes for any reason, nothing works any more in a single stroke, from the light switch to the heating.
Conclusion
Now you have learned the difference. The Internet of Things is one of the most important technological pillars of Industry 4.0. Independent communication between machines enables them to solve problems that previously would have required the assistance of a human being. The Smart Factory with self-optimizing value chains, autonomous robots and 3D printers is appearing on the scene. Things that could have been dreamed of 30 years ago.
But every coin also has a flip side. Such a powerful system with enormous connectivity and external control is an invitation to be misused for economic, strategic and monetary purposes.We are certainly in the midst of Industry 4.0, and the development is unstoppable as well as accelerating. Exponentially fast. Companies must start to invest in their cybersecurity and robust IT right now at the latest.
On the other hand, unforeseen efficiency and effectiveness in production and manufacturing beckons, which can be achieved with the right experts in areas such as data science, artificial intelligence, machine learning and robotics. That' s why we are looking forward to this exciting future with anticipation and optimism.
Related articles:
IT Security in Times of Digital Transformation
Next Level Supply Chain Management – Digitalisation of logistics
The digital transformation of production - Manufacturing 4.0